How DPF Cleaning Machines are Transforming Diesel Engine Maintenance
DPF woes plaguing your diesel trucks? DPF cleaning machines are here to save the day! Learn how they improve efficiency, reduce downtime & save costs for trucking fleets. Embrace the future of diesel engine maintenance!
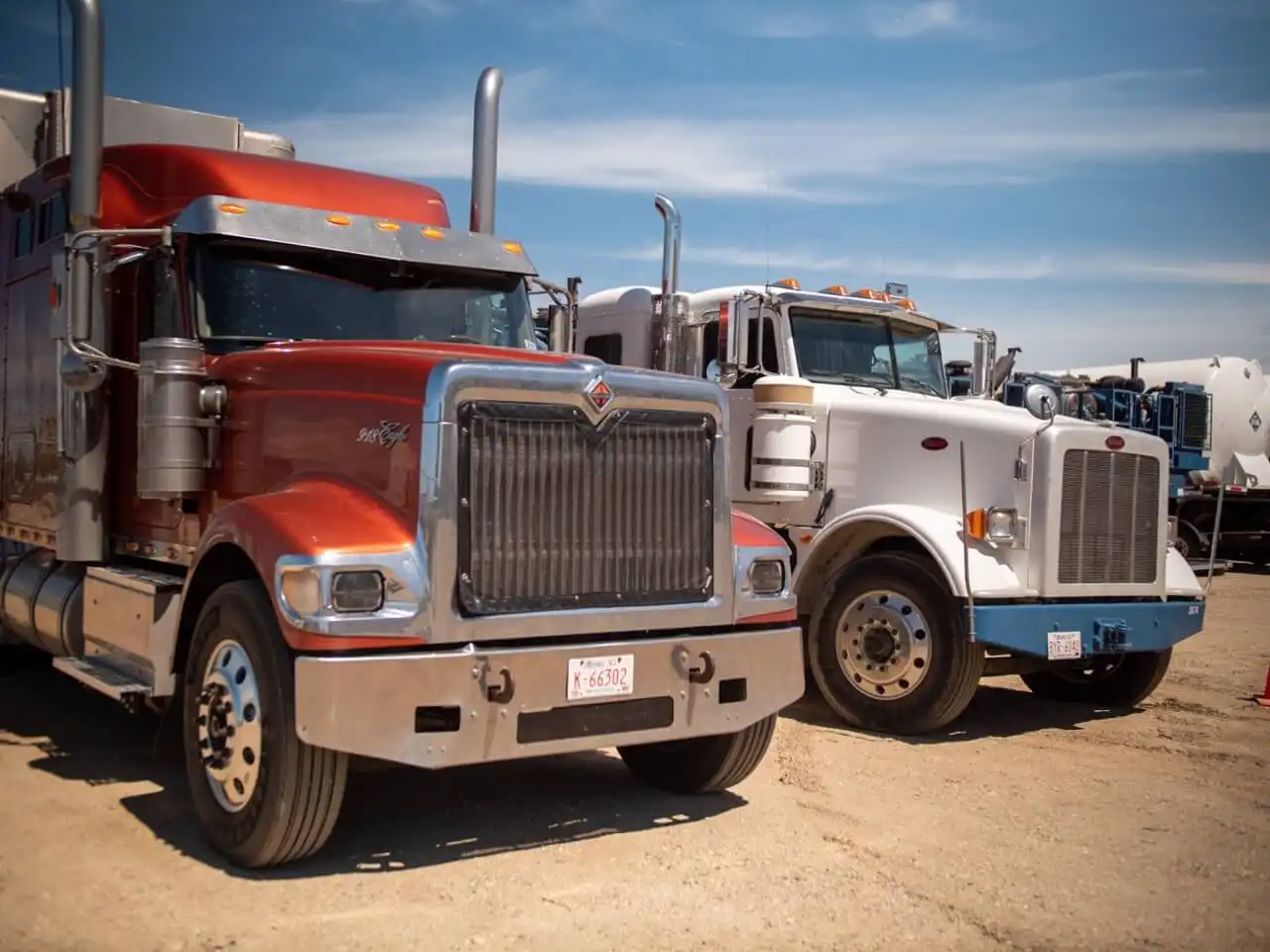
One critical component in diesel engine maintenance is the Diesel Particulate Filter (DPF). Read more to learn about the significance of DPFs, the challenges they pose, and the transformative role of DPF cleaning machines in modern diesel engine maintenance.
To learn more about our DPF repairs at S.E.R. Fleet Services, please visit our DPF Service page here.
Introduction to DPF and its Maintenance Challenges
Understanding DPFs
Diesel Particulate Filters (DPFs) are crucial components designed to trap and remove particulate matter (PM) emissions from diesel engine exhaust gases. These emissions, consisting of microscopic particles and soot, pose significant health and environmental hazards, making DPFs integral to reducing air pollution and meeting regulatory standards. Without effective filtration, these harmful particles can contribute to respiratory illnesses and environmental degradation, emphasizing the role of DPFs in safeguarding public health and preserving air quality.
Common Maintenance Challenges
Despite their importance, DPFs face several maintenance challenges:
- Soot Buildup: Over time, DPFs accumulate soot and ash, restricting airflow and reducing engine efficiency.
- Regeneration Issues: DPFs require periodic regeneration to burn off trapped soot. However, incomplete regeneration can lead to clogging and engine malfunctions.
- High Temperatures: Regeneration processes generate high temperatures, increasing the risk of thermal stress and damage to DPF components.
Cleaning Methods
Traditional cleaning methods for DPFs include various techniques to remove accumulated soot and ash and restore optimal filtration efficiency. These methods include:
Pneumatic Cleaning
This method utilizes compressed air to dislodge and evacuate trapped particulates from the DPF substrate. The high-pressure air pulses through the filter, agitating and loosening the soot and ash deposits. While pneumatic cleaning can effectively remove surface-level contaminants, it may struggle to address deeper clogs and stubborn deposits.
Thermal Cleaning
Also known as heat treatment or thermal regeneration, this method involves subjecting the DPF to elevated temperatures to combust and burn off trapped soot. Thermal cleaning processes typically utilize specialized ovens or furnaces to heat the filter element, facilitating the oxidation of soot particles. While effective in removing accumulated contaminants, thermal cleaning poses risks of thermal stress and potential damage to DPF components if not carefully controlled.
Chemical Washes
Chemical cleaning agents are used to dissolve and break down stubborn soot and ash deposits within the DPF substrate. These agents, often in the form of detergents or solvents, are circulated through the filter, penetrating the porous structure to facilitate the removal of contaminants. While chemical washes can achieve thorough cleaning results, they raise environmental concerns due to the use of potentially hazardous chemicals.
Limitations
Despite their effectiveness in certain scenarios, traditional cleaning methods have notable limitations:
- Labour-intensive: Manual cleaning processes require significant human labor and time investment, leading to downtime and reduced operational efficiency for commercial trucking fleets. The need for skilled technicians to perform cleaning tasks further adds to operational costs and logistical challenges.
- Incomplete Cleaning: Traditional methods may struggle to achieve comprehensive removal of all accumulated soot and ash, especially in hard-to-reach areas of the DPF substrate. Inadequate cleaning can result in suboptimal filter performance, leading to decreased engine efficiency and potential compliance issues with emissions regulations.
- Environmental Concerns: Chemical cleaning agents used in traditional methods can pose environmental risks, including contamination of soil and water sources if not properly handled and disposed of. Regulatory compliance with environmental standards adds complexity and cost to DPF maintenance operations, necessitating careful management of cleaning processes and waste disposal procedures.
The Role of DPF Cleaning Machines
Investing in DPF cleaning machines offers numerous benefits for commercial trucking operations:
- Improved Efficiency: Clean DPFs optimize engine performance, leading to better fuel economy and reduced emissions.
- Reduced Downtime: Automated cleaning processes minimize downtime, allowing trucks to stay on the road and maximize productivity.
- Cost Savings: By extending the lifespan of DPFs and reducing manual labor requirements, cleaning machines offer long-term cost savings.
Real-World Effectiveness
The effectiveness of DPF cleaning machines is underscored by outcomes in commercial trucking operations:
- Fleet Optimization: Trucking companies have reported substantial enhancements in fleet performance and compliance with emissions regulations following the implementation of DPF cleaning machines. These machines ensure that vehicles maintain peak efficiency, reducing emissions and enhancing overall operational performance.
- Maintenance Cost Reduction: Businesses benefit from significant cost savings over time as DPF cleaning machines reduce the frequency of manual cleanings and engine repairs. Companies optimize their maintenance budgets and improve operational profitability by minimizing downtime and labor costs associated with traditional cleaning methods.
- Regulatory Compliance: Meeting stringent environmental regulations is made more manageable and cost-effective with the efficient maintenance facilitated by cleaning machines. By ensuring that DPFs remain in optimal condition, businesses can confidently navigate regulatory requirements while minimizing the risk of fines or penalties associated with non-compliance.
Innovations in DPF Cleaning Technology
Emerging Trends and Innovations
The landscape of DPF cleaning technology continues to evolve, driven by innovation and technological advancements:
- Automation: Automated cleaning systems with remote monitoring and diagnostic capabilities streamline maintenance processes and improve efficiency.
- AI Integration: Artificial intelligence algorithms optimize cleaning cycles based on real-time data, enhancing precision and effectiveness.
- IoT Connectivity: Internet of Things (IoT) integration enables proactive maintenance scheduling and predictive analytics, reducing unplanned downtime and optimizing fleet management.
Shaping the Future of Diesel Engine Maintenance
As diesel engine technology progresses and environmental regulations tighten, the future of DPF cleaning technology holds exciting possibilities:
- Eco-Friendly Solutions: Continued research and development aim to enhance cleaning methods while minimizing environmental impact and chemical usage.
- Integration with Hybrid and Electric Vehicles: DPF cleaning technology is adapting to meet the needs of emerging hybrid and electric vehicle platforms, ensuring efficient emissions control across diverse fleets.
- Collaborative Industry Efforts: Collaboration between manufacturers, regulators, and stakeholders fosters innovation and standardization, driving progress in diesel engine maintenance and emissions reduction.
Recap
DPF cleaning machines represent a transformative solution in diesel engine maintenance, offering efficiency, cost savings, and environmental compliance for commercial trucking operations. As technology advances and regulatory standards evolve, investing in innovative DPF cleaning solutions is not just a choice but a necessity to thrive in the landscape of the trucking industry. Embracing these advancements ensures a cleaner, more sustainable future for diesel engines and the environment.
Contact SER Fleet Service
For professional diesel mechanic service for your light to heavy-duty truck & fleet, visit our shop in Sacramento, CA or take advantage of our extensive mobile repair service radius. Give SER Fleet Service a call, send us an email, drop by the shop, or fill out our service request form today!
Office
Shop
Request Service
At S.E.R. Fleet Services, we make it easy for you to request our services. Simply fill out our online service request form, and we will get back to you as soon as possible to schedule an appointment.
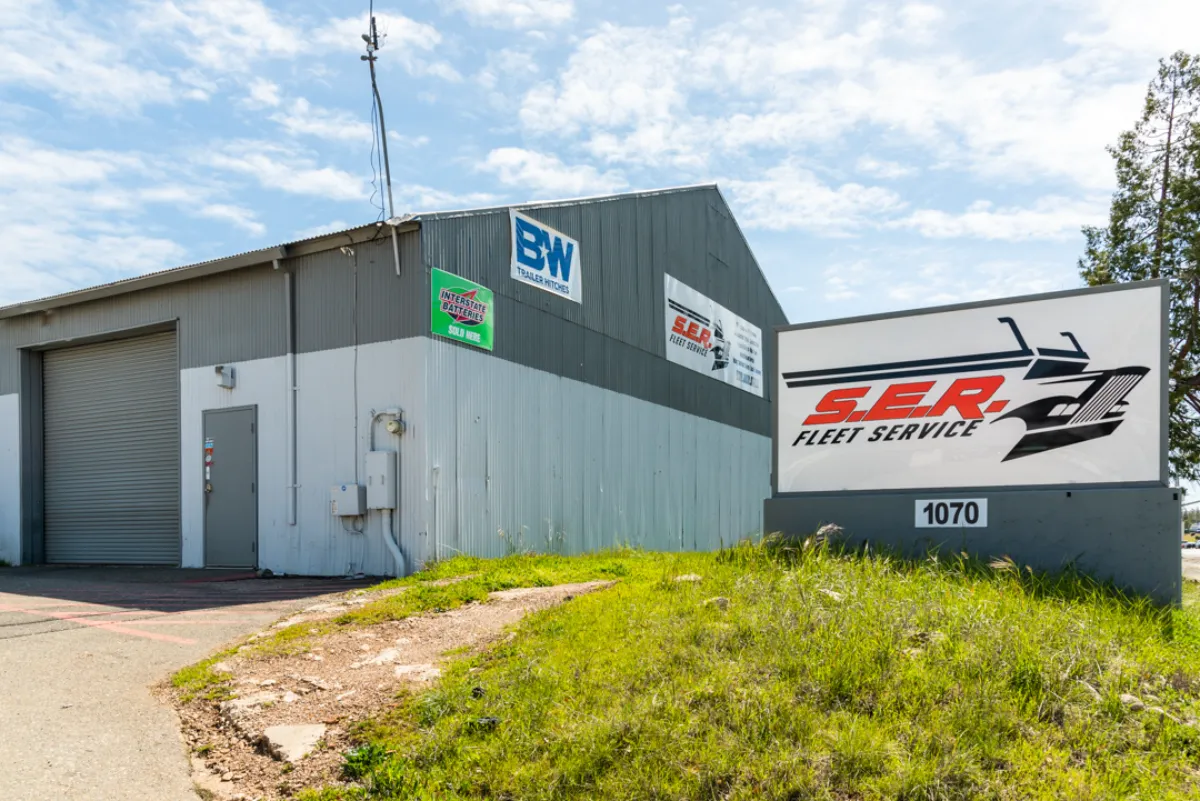